/ Much more than coating
As a full-service provider of surface treatments and manufacturing, we also offer Vacuum Heat Treatment, surface finishing, laser drilling and machining, welding, vacuum brazing and NDT (Non-Destructive Testing) capabilities.
It allows us to deliver customers market-ready parts.
Vacuum HT and brazing
We can process a wide variety of superalloys of turbine engine components, providing coatings with interdiffusion zones and appropriate coating structure. You’re not only assured of state-of-the-art equipment, but also the in-depth experience of our team.
As part of the coating manufacturing scope, we can procure and supply auxiliaries to be vacuum brazed to your products. These include plates, baffles, inserts, deflectors, covers and restrictors to be assembled to your turbine part.
Laser drilling and ablation
When traditional TIG welding is not competitive, or alternative solutions are required to meet weld conditions (such as low heat input, metallurgical aspects, deep penetration in a single pass, repeatability and thick plate welding), LASER welding is the solution.
You can increase overall productivity which may lead you to simplify designs and create stronger components.
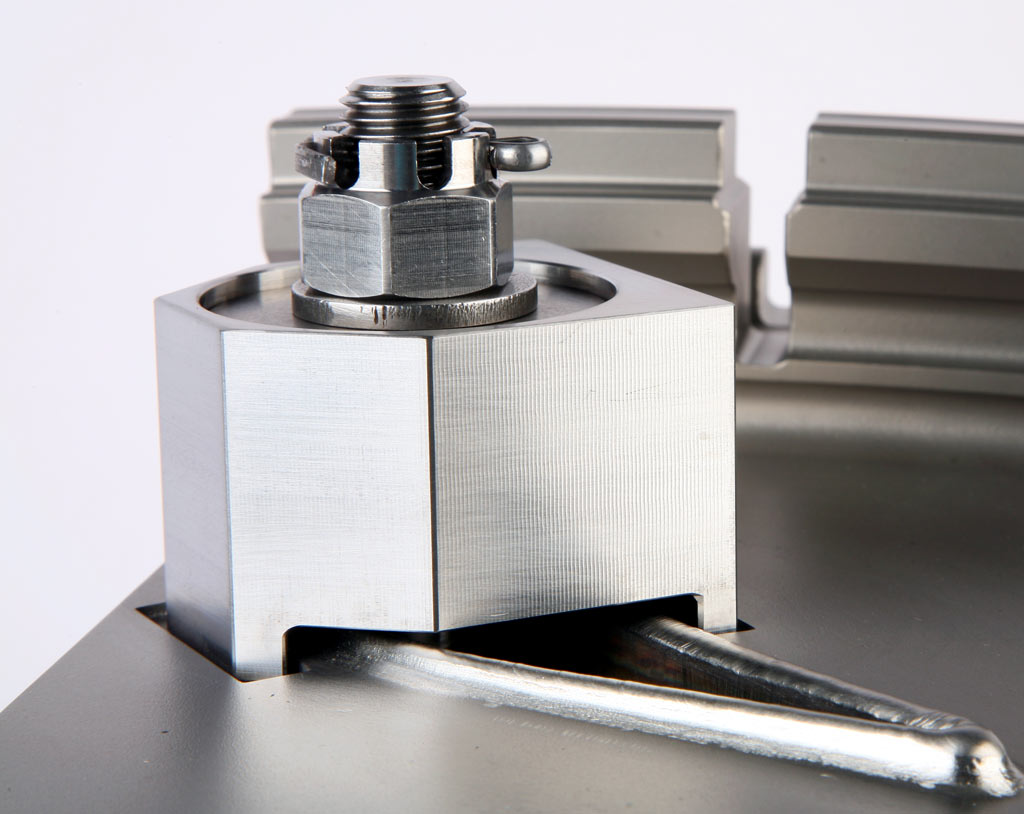
Laser welding and ablation
Laser technology is a core competence, which we offer for drilling through non-conductive TBC coated products with a complex cooling geometry. They may have, for example, a serpentine cooling scheme matched with a pattern of film cooling holes.
Through 3D modelling, probing and optical enhancements of process control, we can offer cylindrical or shaped (fan) hole drilling patterns through a fully coated part. Airflow measurement is an integrated process to check designated flow rates of your products.
Surface finishing and Non-destructive testing (NDT)
- Controlled shot peening
- Surface roughness reduction
- Chemical and dry-ice stripping
- FPI
- Ultrasonic measurements
- Airflow and waterflow
- Metallography
- Eddy current measurements
- SEM Microscopy, XRD and XP
Lincotek Surface Solutions offers a full range of surface finish methods and is at your service to improve performance and overall product quality.
A wide variety of inspection schemes and qualified personnel is available to assess your products and release them in an engine-ready condition.